Screw pump operates with two counter-rotating screw rotors that are carefully designed to rotate “toward each other”. This traps the gas in the space between the rotor “screws”. As the screws rotate, this trapped volume is reduced, which not only compresses the gas, but also moves it toward the exhaust port.
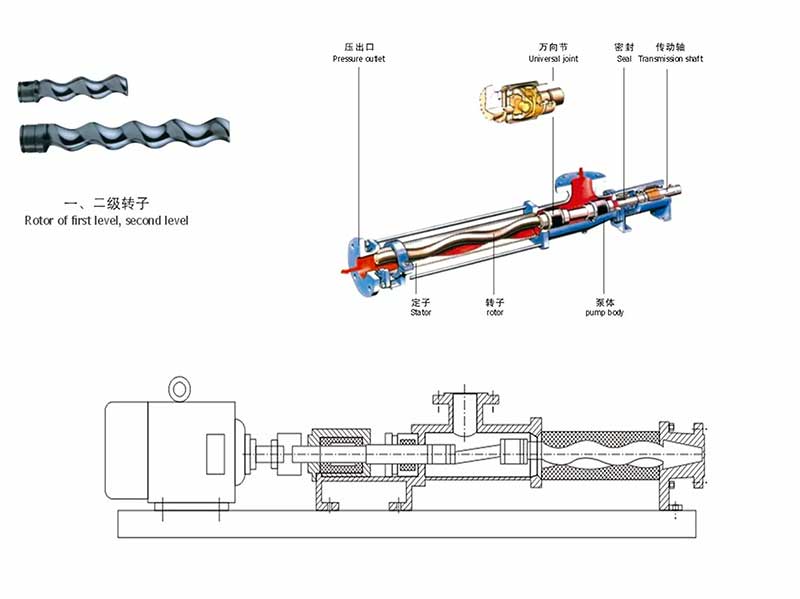
https://www.hw-screwpump.com/products/eccentric-screw-pump/screw pump
When the progressive cavity pump begins to operate, power is supplied to the drive screw via an electric motor. The drive shaft is connected to the screwdriver that drives the screwdriver.
When the drive screw starts to rotate, the driven screws also rotate, as these screws engage each other. Due to the movement of these screws, a minimum vacuum starts to be generated in the inlet section. Due to this vacuum, fluid is drawn into the pump through the inlet valve.
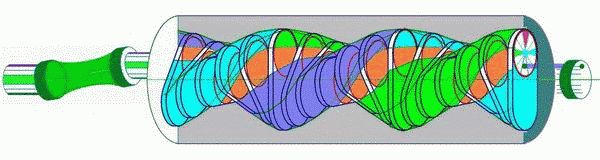
Working principle of screw pump
As the fluid enters the pump, it becomes trapped between the gaps in the “screws”. This trapped fluid also moves with the rotation of the screw. As the screw moves, the volume of the trapped fluid decreases and the pressure of the fluid increases.
As the pressure of the fluid increases according to the desired pressure, it is discharged from the outlet valve and moved to the desired location.
When a screw pump pumps oil or other types of viscous fluids, the screw surfaces are lubricated as the fluid is pumped, so there is little or no clearance between the screws.
However, when pumping gas/water mixtures, water, or other types of light liquids, these components cannot come into contact with each other. If there is no contact, the parts will wear out quickly. Therefore, do not use a triple screw pump (where one screw drives the other two without gears) for water supply or multi-phase operation.