The stator is a crucial component of a screw pump, and it is responsible for creating the chambers that move the fluid through the pump. It is a stationary cylinder with an internal helical profile that matches the rotor’s screw thread. The rotor rotates inside the stator, and the screw thread forms a series of chambers that trap and move the fluid from the pump inlet to the outlet.

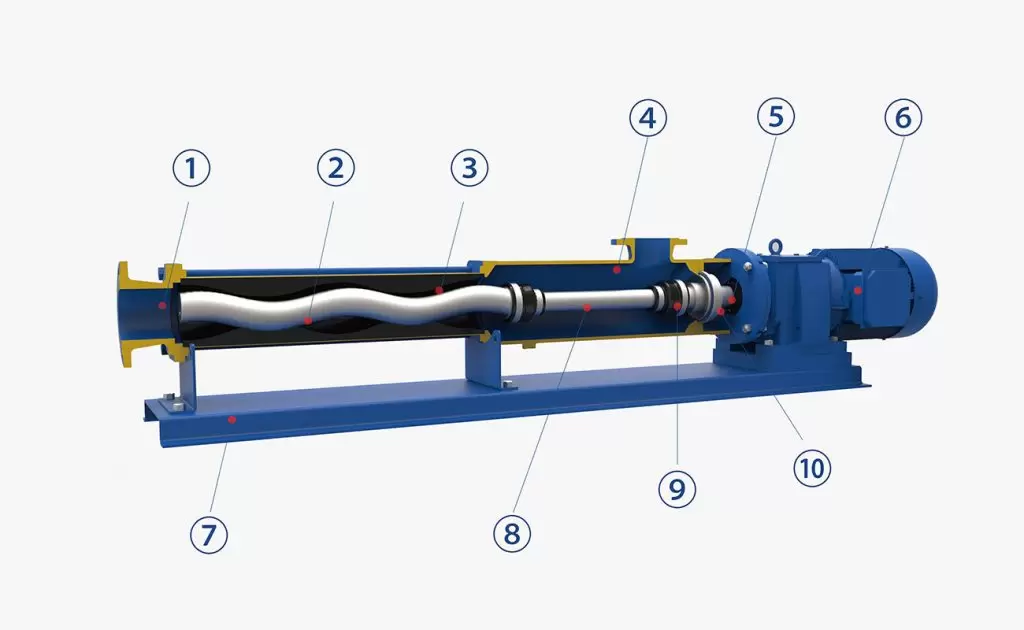
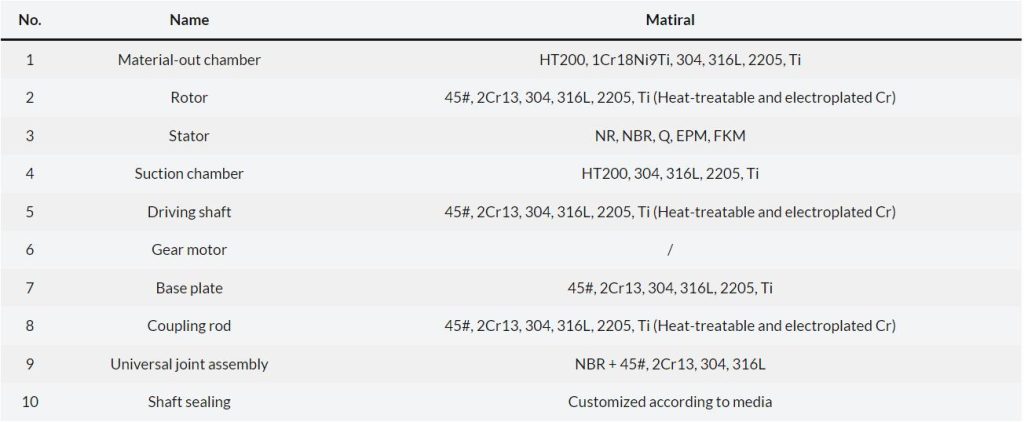
The Stator of a Screw Pump
The stator is mostly made of rubber. Because it needs to form a closed meshing cavity with the rotor, it is an interference fit with the rotor. When the rotor (main shaft) rotates and causes continuous friction, it will wear naturally.
The geometry of the stator’s internal profile is critical to the pump’s performance. It should be closely matched to the rotor’s helical screw thread to minimize clearance between the two components. The clearance should be minimal to ensure that the fluid is effectively trapped and moved along the screw thread without any leakage.
The stator’s material is also essential to the pump’s performance and longevity. Stator materials should have high wear resistance, corrosion resistance, and mechanical strength. Common materials used for stator construction include rubber, elastomers, and various polymers.
The stator’s design also affects the pump’s performance. For example, some screw pumps have stators with an elongated profile, while others have a shorter profile. Longer profiles tend to generate higher pressures, while shorter profiles tend to generate higher flow rates.
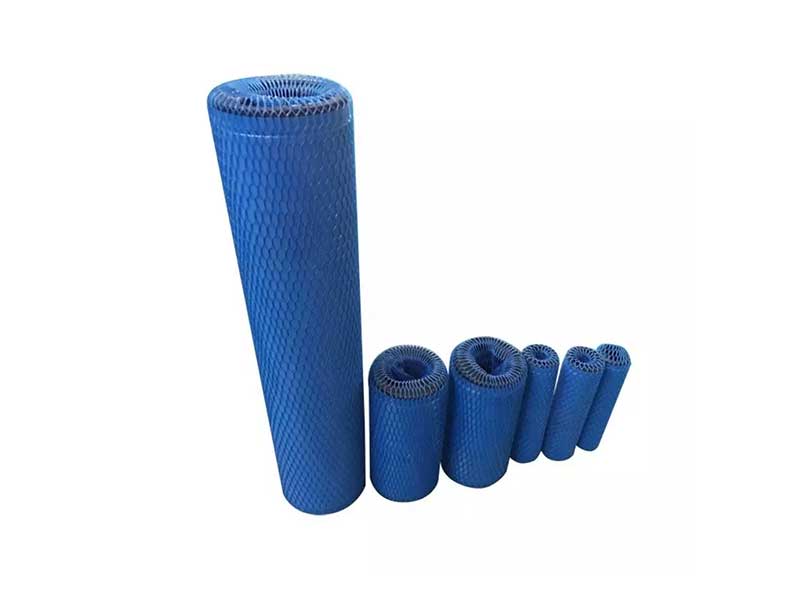
Another critical factor that affects the pump’s performance is the stator’s surface finish. The surface finish should be smooth to minimize friction between the stator and rotor, which can lead to wear and reduced performance.
The stator’s size also affects the pump’s performance. Generally, larger stators generate higher pressures, while smaller stators generate higher flow rates. However, the stator size should be optimized to balance performance and efficiency.
Proper maintenance and care of the stator can ensure optimal pump performance and longevity. Regular cleaning, inspection, and replacement of worn or damaged stators can help extend the pump’s lifespan and prevent downtime.
In conclusion, screw pump stator is a critical component of a screw pump. Its geometry, material, design, surface finish, and size all affect the pump’s performance and longevity. Proper maintenance and care of the stator can ensure optimal pump performance and prevent downtime.

Natural wear:
Under the same working conditions, natural wear is divided into the following:
- Wet abrasive wear is a condition of particle wear, that is, the conveyed medium contains particles, and there is a liquid medium between the abrasive particles and the rubber.
2.Fatigue wear is caused when the friction and contact stress between the stator rubber and the blunt mating surface of the rotor are not too large. This kind of wear is similar to abrasive wear in many aspects. Some scholars regard fatigue wear as a form of abrasive wear, that is, blunt abrasive wear. But compared with abrasive wear, fatigue wear is a low-strength wear.
Erosion wear is also known as erosion wear. This wear occurs due to the liquid flow between the screw pump rotor and stator. This type of wear is one of the main forms of wear during the normal operation of the screw pump.

How to disassemble and replace screw pump rotor or stator?
Here are some common questions and answers about screw pump stators:
Q: What is a screw pump stator?
A: A screw pump stator is the stationary component of a screw pump that houses the rotating screw pump rotor. The stator has a unique geometry that creates a sealed cavity with the rotor, which moves fluid from the pump’s suction to discharge side.
Q: What materials are screw pump stators typically made of?
A: Screw pump stators are commonly made from elastomers, such as natural rubber, synthetic rubber, or thermoplastics, depending on the application requirements and the fluid being pumped.
Q: What are the different types of screw pump stators?
A: Screw pump stators come in various geometries, including single helical, double helical, tri-helical, and other configurations. The geometry of the stator can affect the flow rate, pressure, and efficiency of the pump.
Q: What are some advantages of using a screw pump stator?
A: Screw pump stators offer several advantages, including the ability to handle fluids with varying viscosities, low pulsation flow, and high volumetric efficiency. They are also capable of handling abrasive and corrosive fluids.
Q: How do I select the right screw pump stator for my application?
A: To select the right screw pump stator, you should consider factors such as the type of fluid being pumped, the pump’s flow rate and pressure requirements, and the temperature and viscosity of the fluid. Consulting with a pump specialist can also be helpful in selecting the appropriate stator.
Q: How do I maintain and replace a screw pump stator?
A: Regular maintenance is essential for prolonging the life of a screw pump stator. This includes cleaning the stator and rotor, inspecting for wear and damage, and replacing worn or damaged components. Replacement stators can be purchased from the pump manufacturer or a third-party supplier.
Q: Are there any common problems with screw pump stators?
A: Common problems with screw pump stators include wear, cracking, and swelling due to exposure to certain fluids or temperatures. Regular maintenance and proper material selection can help minimize these issues.
In conclusion, screw pump stators are essential components of screw pumps and offer several advantages for pumping fluids in various industries. Proper material selection, regular maintenance, and replacement when necessary can help ensure efficient and reliable pump operation.
